Failure of a weld can have serious consequences. A weld failure in the backyard of house may not have much consequences. However, when the weld lies in a large sized pressure retaining equipment, weld failure can cost heavily on life and equipment. Such failures have to be analysed by an expert or a team of experts, who carry out an investigation into the causes behind the failure.
In the non-critical welds too, it is important to understand the causes of failure so that a repetition of weld failure can be avoided.
Such an investigation must be thorough, and scientific, so that the right causes can be captured. This is required so that failures can be prevented from re-occurring. In order to do a sound investigation, the expert must have good knowledge on welding techniques, NDE techniques, and metallurgy.
The expert must take into account all information available, right from design, fabrication sequence of the component, and operating parameters of the component. Any factor that could have remotely contributed to failure must be taken into account.
An investigation in weld failure must take into account the metallurgical make-up of the weld, the service life of the component, conditions that might have led to the failure, and the mode of failure. Often the information revealed by such an investigation leads to largescale changes in the design, fabrication sequence, operating parameters of the equipment. Such information leads to advancement of knowledge. The study therefore, must be done capably – as this allows us to build a more reliable product in future.
In this article, we shall discuss how to objectively approach such an investigation. How do we go about doing it, how to establish findings and results?
Areas Of Focus
Any investigation focusses on the following factors while going about analysing a weld failure: Initial observations, background data, laboratory studies, and welding failure analysis. This helps us in determining the causes of failure and interplay of factors, if any. Let us see these factors in brief.
Initial Observations
When a welding failure occurs, the expert investigating it must first inspect the site of failure and record his initial observations. This inspection should be made as early as possible after the failure has occurred. The observation can be in the form of notes, and photographs of all parts the captures the texture and location of failure surfaces.
The initial observations must also include interviews with the witnesses.
Background Data
The investigator then collects an in-depth back ground information about the failed weldment. This information may include design aspects of the joint, methods of fabrication, weld procedures, welding consumables used to make the joint, post weld heat treatment, repairs, operating parameters of the part, normal loading, possible abuse – inadvertent or otherwise, maintenance schedule, etc.
An effort should be made to collect all information that might point to the causes of failure.For example, the fabrication sequence may have recorded a non-conformance which might not have contributed to the failure, but should be recorded nonetheless to draw up a holistic picture.
Laboratory Studies
The investigator then subjects the failed surfaces to a few tests such as chemical composition, macrograph or micrograph of the failed surface. The chemistry check allows him to ascertain whether the part actually possess the composition indicated by the welding procedures. A micrograph tells about the microstructure of the part. This allows the expert to correlate he microstructure on the failed part with that recorded during fabrication sequence.
The laboratory tests add to the whole picture, and give more information to the investigator so that he can form a holistic view.
Weld Failure assumptions
Following the compilation of background data and laboratory tests, the investigator then makes assumptions about the causes that might have caused the failure. These assumptions may be made by taking into account not just the pieces of information available, but also the pieces that are not available. The assumptions must then be tallied with the available evidence to determine the cause of failure.
Causes Of Weld Failure
Failure in welds can occur due to one of the following factors:
- Failure due to an error in design of the equipment by the designer. In other words, faulty design.
- Failure due to an error in fabrication of the equipment. For example, use of wrong filler rod, non-adherence to specified welding procedure, non-conformance in post weld heat treatment, and so on.
- Failure due to deterioration of the part in operating conditions.
Let us examine each of these three factors in some detail.
- Failure due to error in design: A faulty design can occur due to ignorance on the designer’s part, or plain oversight. A faulty design can involve incorrect calculations, or inadequate stress analysis, or assumption of static loading instead of dynamic loading or fatigue loading. A ductile failure can occur due to overloading of the part than what the strength of the material permits. A brittle fracture can occur to a wrong choice of the material, or presence of stress risers in the design.
- Failure due to error in fabrication: These type of errors can involve use of incorrect filler metal, wrong joint design, or inadequate preheat temperatures, or lack of post heating, unacceptable non-conformance in post weld heat treatment cycle. Such mistakes may also involve presence of weld defects such as incomplete penetration at the root, slag inclusion, lack of fusion with the sidewalls, and wrongful acceptance by the quality inspector.
- Failure due to deterioration of the part during service: Normal wear and tear occurs during the service that is generally accounted for during the design. In-service inspection of the parts is specified for critical parts. If appropriate action is not taken on the actionable points thrown up by the in-service inspection, it can also act as a factor that contributed to failure. If action is taken, but the action is not technically adequate, that needs to be examined too. Further, if a part gets corroded due to ambient conditions, then such damage gets accentuated by the presence of stress concentrators, and can lead to failure. In-service cracking is discussed in further detail in the following paragraphs.
We shall examine a few commonly occurring types of failures in weldments such as in-service cracking, brittle fracture
In-Service Cracking
The weldment may develop cracks during its’ service due to a variety of reasons. These reasons could be stress corrosion, cold-cracking, or fatigue failure, or graphitization, etc. As we know, a weldment contains a relatively hard micro-structure in the heat affected zone. Moreover, residual stresses are found in any weld. The residual stress, hard microstructure in HAZ, and the aforementioned factors may combine to produce cracking during the service of the part.
Failure of a part may occur due to many other reasons that are not attributable to welding. An overall analysis of failure would be much wider in scope. In the below paragraphs, we shall limit ourselves to analysis of failure in weldments.
Below, we shall see the four types of failures that can occur in a weldment during its’ service: brittle fracture, fatigue fracture, lamellar tearing, and stress corrosion cracking.
Brittle Fracture
Fractures are ordinarily of two types: Brittle fracture and ductile fracture.
Ductile fracture is accompanied by a deformation of the structure. That is, the material yields first – before undergoing fracture, similar in the manner to the fracture of a mild steel tensile specimen in the tensile test. Yielding or stretching is accompanied by a reduction in cross section area of the part as well.
The figure below depicts a ductile fracture surface.
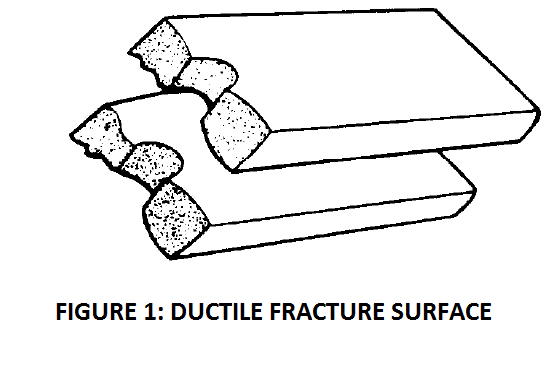
Brittle fracture on the other hand, occurs by cleavage across the individual crystals. The fracture exposes the granular structure of the metal, and it is not accompanied by any yielding or stretching of the metal. Consequently, there is no reduction in the cross section area either.
The figure below depicts a brittle fracture surface.
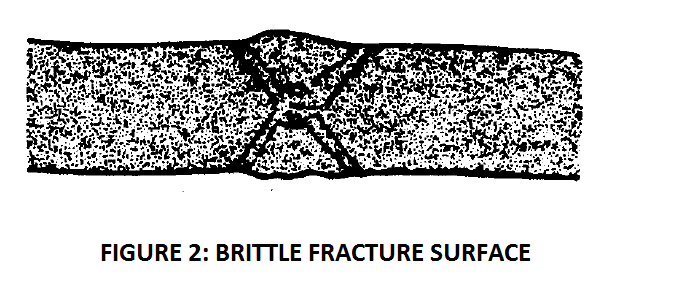
How To Identify A Brittle Fracture
Generally, while inspecting a fracture surface, one notices that the surface exhibits characteristics of both ductile and brittle surface. Sometimes, it so happens that the fracture changed its’ mode of fracture during the propagation of fracture. Such surfaces will exhibit both characteristics. For analysing a brittle fracture, it is important to identify one first.
There are four factors that help us in identifying a brittle fracture: growth markings on the fractured surface, mode of fracture, texture of the fractured surface, and amount of plastic deformation at the fracture surface.
Growth Markings
Growth markings are lines on the fracture surface that help in identifying the type of failure. These markings are one of the ways to identify the type of fracture. It should be noted that not all types of fracture produce growth markings.
On a fatigue fracture surface, there are fine lines of increasing dimension, and of fine texture, that are produced by gradual growth of the crack as it increases in dimension.
A herringbone pattern is formed in the case of brittle fractures. The apex of the herringbone pattern points towards the origin of the crack. This reveals the direction of propagation of the crack.
Fracture Mode
Ductile materials fail by the shear mode of crystalline fracture. The surface of ductile fracture spears silky or fibrous. The fracture surface falls at an angle of 45° to the axis of external load applied.
Fracture Surface Texture
The texture of the fracture surface is granular or crystalline in appearance for a brittle fracture. A herringbone pattern points towards the origin of fracture. For a ductile fracture, the fracture surface has a dull texture.
Amount Of Plastic Deformation
The amount of deformation undergone by the part also indicates the type of fracture. We know that, ductile materials undergo some degree of plastic deformation before getting fractured. Necking can be seen in the material at the point of fracture.
On the other hand, brittle materials get fractured in one go, without any deformation or yielding in the material, and without formation of any necking in the fracture zone.
Other Characteristics Of Brittle Fracture
Another characteristic of brittle fracture is that it occurs in one jerk. The material breaks suddenly without any fore-warning. The crack propagates at a rapid pace through the material. Imagine a piece of glass breaking into pieces. A glass is a highly brittle material.
The failure often occurs at stresses that are below the yield stress of the material.Even a material that exhibits ductile behaviour during tensile test at room temperature may develop a brittle fracture. A material having good toughness at room temperature may develop brittle fracture, under certain conditions.
Let us try to understand the conditions which set up a material to undergo brittle fracture. Once we understand these conditions, we can try to eliminate some of them to reduce the possibility of a brittle fracture.
Conditions For A Brittle Fracture To Occur
In order for a material to fail by way of brittle fracture, the following conditions must exist: low temperature, a notch or defect that may initiate a crack, presence of tri-axial stresses in the material, and a relatively high rate of loading. The microstructure of the metal also has a significant effect on the type of fracture.
Let us understand these conditions in brief.
Low Temperature
If we subject a number of specimens extracted from a material to impact tests at a range of temperatures, we can draw a few conclusions. As the temperature decreases, the impact energy absorbed by the material decreases. As the temperatures decreases further, the percentage of ductile fracture surface on the broken specimen decreases.
The mode of fracture increasingly becomes brittle.There comes a temperature, when the material becomes almost fully brittle, and the impact energy absorbed by the specimen is quite less. This temperature is called ductile-to-brittle (DBT) transition temperature.
The lesson is that even ductile metals turn brittle when taken to low temperatures. So, if a crack inducing notch is present, and other fracture conducive conditions are available, even a ductile metal may undergo a brittle fracture at low temperatures.
Presence Of A Notch
The presence of notch or a defect is necessary for a brittle fracture to occur. In tests such as impact tests and drop weight tests, such a notch is purposefully made in the test specimen so that the specimen is induced to crack. The resistance posed by the metal to the propagation of the crack indicates the toughness of the metal, or the ability to resist brittle fracture.
In actual parts however, a notch is not intentionally made. It may exist in the form of a defect that may occur due to a faulty design or an error in the fabrication activity.
The notch acts as the site of stress concentration. This invites fracture to occur by brittle mode, with no chance for yielding to occur.
Rate Of Loading
The term rate of loading indicates the rate of strain versus time. When the material is subjected to a high rate of strain, it does not allow the normal slips in the material to occur. This happens when the material is subjected to shock loading.
When such loading conditions occur, and a notch is present in the material, the material under the notch gets subjected to very high stresses. This leads to a sudden failure of the structure. A fracture happens at a very fast rate that gives no time to the people nearby to react.
Tri-axial Stresses
The presence of tri-axial stresses, which occur with more likelihood in thicker materials, is conducive to the brittle fracture. Thicker materials are more likely to have less ductility in the through thickness direction.
Microstructure Of The Metal
The microstructure of the metal plays a major role in determining the type of fracture. The microstructure depends on the chemical composition of the metal and heat treatment given to it. For weldments, it also depends on welding procedure.
The method of fabrication also plays a role. The manufacturing operations such as forming, punching, flame cutting, flame welding, etc. affect the microstructure such that the ductile to brittle transition temperature of the material is raised. In other words, the material is drained of its’ ductility at a relatively higher temperature than what would normally be the case.
The right heat treatment after welding (or any other fabrication activity such as cold working) produces a grain refinement which has higher toughness than a microstructure having coarse-sized grains.
How To Reduce Possibility Of Brittle Fracture In Weldments?
Welding is a necessary evil. If we had a choice, we would cast all the required components. However, clearly – casting is not always possible. In complex parts, there is simply no way but to resort to welding.
Welding gives rise to occurrence of hard coarse-grained microstructure in the heat affected zone, which is more susceptible to brittle cracking than other regions. HAZ has a higher DBT temperature than other portions of the weld. This is undesirable.
Also, welding is always accompanied by residual stresses. If these stresses are of the order of yield strength of the metal (which, in the cases of thick base metal – it might very well be!), it is an invitation to cracking. The weld defects, which are impossible to eliminate completely, may acts as the site for start of a crack.
However, be that as it may, we must live with welding. It is possible to take steps to reduce the possibility of brittle fracture in a weldment to a large extent.
One way to do this is to select appropriate grade of base metal that possess adequate toughness at the service temperatures of the equipment. The DBT temperature of the metal should be well below the service temperature of the equipment.
A mind boggling variety of alloys exists in the world that have mechanical properties to suit the requirements of most applications.
Another way to reduce the possibility of cracking is to do appropriate heat treatment after the welding. Heat treatment relieves the residual stresses built up in the volume of the metal after welding. Some heat treatments also serve to refine the grain size of the weld metal. This increases the toughness of the metal.
Another way is to design the part such that there are no notches or sites of stress concentration in the body of the part.
Another way is to ensure a defect free weld. For this, the approach must combine an optimum welding procedure, as well as deployment of skilled welders.
Fatigue Failure
Sometimes, the loading on a part is such that the metal undergoes opposite types of loading one after another, repeatedly, which goes on repeating for a large number of cycles. For example, the metal may undergo tensile stress and compressive stress, one after other, repeatedly, for large number of cycles.
This kind of loading produces fatigue in the part. To understand this better, imagine a load bearing shaft that rotates at high speed. Under the load, the fibres of the shaft body that are at the top at an instant would be under compressive stress, while those at the bottom would be under tensile stress. The situation is reversed when the fibres that were at the bottom at an instant earlier come to the top. This change of stress at the metal fibres acts very rapidly; for a shaft rotating at 500 rpm, this change occurs more than eight times per second!
Assume that the shaft needs to remain in service for several years. The number of cycles that the shaft needs to tolerate with such changing loads is very large. Under such conditions of changing loads or fluctuating loads, the material undergoes what we call as fatigue.
Due to fatigue, a part undergoes failure at a stress that is much below the yield stress of the metal obtained during the ordinary tensile test. Such failure is attributable to fatigue. After incurring considerable fatigue, the material exhibits very little or no ductility. Hence a brittle fracture occurs.
Fatigue failure occurs when a crack forms and propagates due to repeated changing or fluctuating load. When the crack increases enough in size, the load carrying capacity of the part decreases. The fatigue induced cracks may exist in some welds, but the failure does not occur till load carrying area is reduced.
Fatigue does not subside or disappear in periods of inactivity. It is a cumulative effect which is ordinarily not possible to reverse.
The crack increases in size progressively as the number of cycles keep repeating. The rate of progression of crack depends on the rate of loading, type of material, etc.
The surface of a fatigue failure is characterised by a smooth texture, with the presence of concentric rings spreading from the point where the crack initiated.
The direction towards the increasing radius of rings indicates the direction of propagation of crack. The surface becomes less smooth as the rate of propagation of crack increases, which it does towards the end.
The figure below shoes the surface of a fatigue fracture.
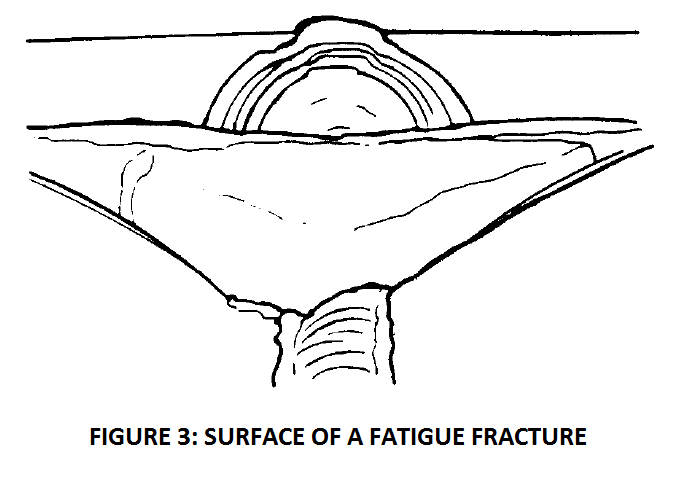
A structure that has been designed keeping static loads in consideration, and based on the yield stress of the material, will not perform as expected when it is subjected to cyclic loads or fluctuating loads. So, the loading of the part during service should be clearly envisioned during the design stage.
Fluctuating loads can vary from oscillating loading such as those in a shaft. Or, the fluctuating loads can be any randomly varying loads. Such dynamic loading can be of various types. It can be alternating tensile and compressive loading. Or it can be a pulsating loading going from tensile stress to no stress, and back to tensile stress again, and repeating thus thereafter.
Or it can go from no stress to compressive stress, back to no stress, and repeat thus thereafter. Besides the magnitude of loads, number of cycles also needs to be taken into design calculations. Normally, number of cycles is taken in terms of millions of cycles.
When the structure has to be designed for such dynamic loading, simple yield stress combined with a factor of safety is not enough. Fatigue stress, in fact, has to be taken into account.
Testing rigs are available to subject specimens to millions of test cycles. The results are plotted on stress versus number of cycles in millions. The test conditions may not be as adverse as the actual service conditions. Therefore, all such factors that could impact fatigue life of a weldment should be taken into account during design.
Factors Behind Fatigue Failure In A Weldment
The fatigue failure of a weldment depends on four factors:
- Type of material used.
- Number of loading cycles.
- Stress level and nature of stress variations.
- Design details of the part.
The design for a part that is slated to undergo fluctuating loading must ensure a uniform stress distribution in the part. The weldment should be specified to have full penetration. The inspection of a welded part should ensure that no complete root fusion has taken place. Excess penetration is not desirable too. Slag inclusions, incomplete fusion with side-walls, etc. can also act as sites of stress concentration.
So, all in all, correct design coupled with skilled workmanship are our defences against fatigue failures.
Lamellar Tearing
Lamellar tearing is a type of cracking that occurs inside the base metal, usually outside the heat affected zone of the weld, and generally parallel to the fusion line of the weld. It generally occurs in weldments made on rolled steel plates.
See the following figures for an illustration. A line on the left of the weld represents lamellar tearing.
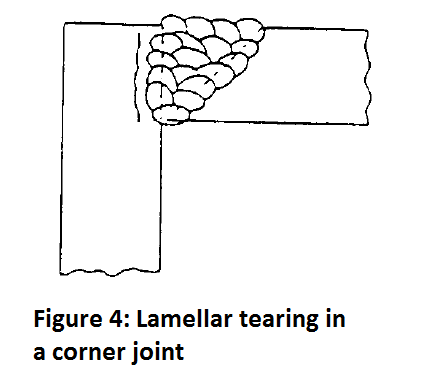
Here is another illustration.
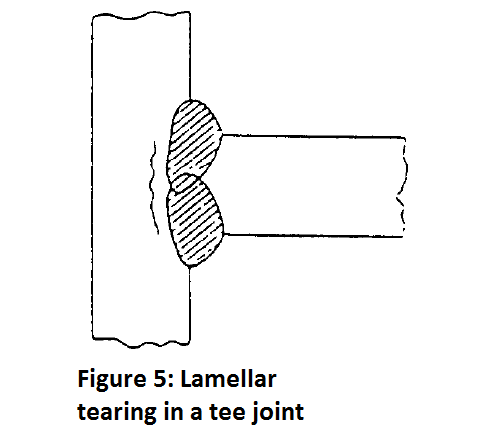
This type of cracking is often found in the T joints such as those shown above. The shrinkage undergone by the bulky weld metal in the T joint exerts a pull on both the base metals. One of the base metals, which is a rolled plate, has a pre-existing tear that tends to open up due to this pull.
A tensile load thus acts on the tear in the Z-direction of the weld, that is in the through thickness direction of the plate on the left in above figure. The small tear may become big, and this is the genesis of lamellar tearing.
This type of tearing can be detected by ultrasonic testing. When it is detected, it needs to be repaired by gouging out metal, and re-filling it with a suitable filler metal. If ultrasonic testing did not exist, it would be difficult to detect these cracks. Even with ultrasonic techniques, these types of cracks are somewhat difficult to detect.
Another way to find such a crack is when the part fails, and the section gets uprooted from its’ place during loading.
Conditions For Lamellar Tearing To Occur
In order for lamellar tearing to occur, three conditions must occur. These conditions are:
One, A strain must exist in the through thickness direction of the part. This strain can get caused due to shrinkage of weld metal, or residual stresses left behind after welding, or loading on the part.
Second, a stress must exist in the through thickness direction perpendicular to the weld orientation in which the fusion line of the weld is roughly parallel to the lamellar tear.
Third, the metal has poor ductility in the through thickness direction.
When Does Lamellar Tearing Occur?
In the context of lamellar tearing, it is the low strength of the material in the z-direction that contributes to the problem. Rolled plates have requisite strength in the direction of rolling, but the strength in the z-direction is not as much. The heating done by the welding work and the shrinkage stressing arising from that trigger the problem.
Lamellar tearing is more prone to occur when the thickness of the weld metal is high, because the pull exerted by the bulky weld metal is high. It is to be noted that the lamellar tearing is not same as the under-bead hydrogen cracking.
Lamellar tearing is not a very common occurrence. It only occurs where the combination of the presence of a linear tear just under a T-weld joint occur. Three conditions must occur for lamellar tearing to happen: restraint in the weld joint, joint design, and condition of the base metal.
As we saw above, the possibility of occurrence of lamellar tearing in a tee-joint is high. Suitable alterations can be done in the joint preparation of such joints. For example, a double sides tee joint, welded from both sides, presents a lesser risk than a one sided joint.
In corner joints, as shown in figure 4 above, lamellar tearing advances to the edge of the base metal, and can be readily detected with the naked eye of surface NDE-techniques. In such joints, a slight bevel can be made in the joint design of the corner joint such that the pull exerted by the weld metal would not be perpendicular to the tear. This is illustrated in the figure below.
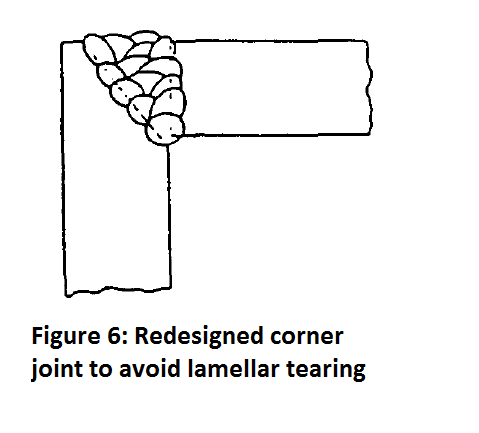
In butt joint, lamellar tearing is generally not much of an issue.
When a filler metal of low yield strength is used, it is likely to reduce the possibility of lamellar tearing as well. This is because the weld metal is likely to respond to residual stresses by yielding, thus reducing the chances for cracking.
One of the common methods to reduce cracking due to lamellar tearing is the buttering method. The surface of the base metal is buttered with a high ductility weld metal of thickness of two to three layers. The groove fillet weld with the second base metal is then made over this buttered surface.
This causes the shrinkage stresses exerted by the groove joint to apply on the buttering, instead of the base metal. Since buttering does not have any pre-existing lamellar tears, the possibility of lamellar tearing comes down significantly.
Hydrogen Induced Cracking
Hydrogen induced cracking occurs when the diffusible hydrogen in the weld metal exceeds the level that the microstructure can dissolve. When the weld metal is deposited, hydrogen may enter the weld metal from various sources such as moisture contained in the electrode coating, base metal surface, humidity in the atmosphere, and so on.
In the molten state, the hydrogen is present in the nascent state, that is, in atomic state. Also, at high temperatures the solubility of hydrogen in the weld metal is high.
As the weld metal cools down, the nascent hydrogen combines and forms molecular hydrogen. As the cooling progresses, the temperature of the weld metal comes down. The solubility of the hydrogen in ferritic microstructures is low (in comparison to the high temperatures). So, the hydrogen tries to escape out. If enabling conditions exist for hydrogen to escape out, it does so harmlessly.
If enabling conditions do not exist, hydrogen gets trapped in the weld metal, and later on cuts through the metal when conducive conditions for cracking occur. Such cracking is called hydrogen induced cracking, since it is primarily driven by the dissolved hydrogen in the microstructure.
Such cracking can occur a few minutes after welding, or few hours, or a few weeks, or after even a few months after completion of welding. Due to this reason, this type of cracking is called delayed cracking. It often occurs when the metal has becomes cold, after completion of welding. Due to this reason, this cracking is also called cold cracking.
Three main conditions must be present for HIC to occur: a hard microstructure (which prevents hydrogen to escape out harmlessly), an external loading (which induces a crack to propagate), and presence of excess dissolved hydrogen in the microstructure (which it can’t tolerate, so the hydrogen must leave, thus cracking the metal).
There are several strategies to tame HIC.
Preheating of the weldment, post heating after the welding at a temperature around 550°F (300°C) (so that hydrogen can escape out harmlessly, rate of diffusion of hydrogen at this temperature is high), baking of the electrodes at 212°F (to drive out moisture from the flux covering), baking of the flux – if submerged arc welding process is used (again, to drive out the moisture from flux), etc. are some of the strategies used to counter hydrogen cracking.
Stress Corrosion Cracking
Stress corrosion cracking, also called caustic embrittlement, occurs when the metal part comes in contact with a corrosive medium and also has stress acting on the part, which induces the propagation of stress.
The stress may occur due to external load acting on the part during service, or residual stress remaining as a result of welding.
The level of stress in the part and the concentration of the caustic solution must be high for stress corrosion cracking to occur. The situation can be remedied by reducing the level of stress in the part, and reducing the concentration of the corrosive medium in contact with the metal part. The concentration of the corrosive medium can be reduced by adding inhibitors to it, which reduce its’ concentration.
So this was about weld failure analysis. Please share your thoughts in the comments section below.