Warpage in welding and residual stresses occurring in welds are a nuisance for any welding engineer. The distortion spoils the aesthetic appeal of the product, and affects its usability for the intended purpose. Residual stresses can give rise to initiation of fracture in the metal, which can result in catastrophic failure.
Therefore, it is important to understand why these phenomena happen, and how to control them. This article will address what is warping in welding, how it occurs, causes of distortion or warpage in welding, types of distortion, and ways to control it.
Also, warpage and distortion in welding mean almost the same thing. Hence, in this article, these terms have been used interchangeably.
What is warpage in welding?
Warpage definition in the dictionary says that it is the result of being bent or twisted out of shape, typically as a result of the effect of heat. In welding, the warpage meaning is same.
Due to the heat involved in welding, the base metal gets distorted out of shape. This spoils not just the aesthetic appeal of the joint, but also renders the component unusable for its intended application. The extent of distortion depends on various factors which we shall see later in this article.
Causes Of Warpage in Welding
First let us see what causes warpage or distortion in welding.
When a piece of metal is heated to a high temperature, it expands equally in all directions. This is the property of metals. Likewise, when it cools – it wants to contract by the same amount in all directions. In welded joints, the weld metal that is cooling down from its’ molten state is not allowed to contract in all directions – since it is integral with the base metal.
As a result, the metal distorts – because cool it must, and therefore contract it must. This is – in simple terms – the reason behind distortion, warpage, and residual stresses in welding.
The amount of expansion and contraction is directly proportional to the amount of temperature change. The change in dimensions of the metal depends on a physical property of the metal, which is denoted by its thermal coefficient (α).
Restating the case – in welding, the weld metal is not unrestrained. So it cannot shrink equally in all directions. This is because it is part of a larger piece of metal that is not heated to the same temperature as a whole. This non-uniform heating, differential cooling, and partial restraint is the main cause of thermal distortion and warpage that occur in welding.
This may be illustrated by a simple example. See the figure below. When this cube is heated, it expands – as shown – equally in all directions. Likewise, when it cools, if it is unrestrained – it contracts equally in all directions. In this cube, no distortion would occur.
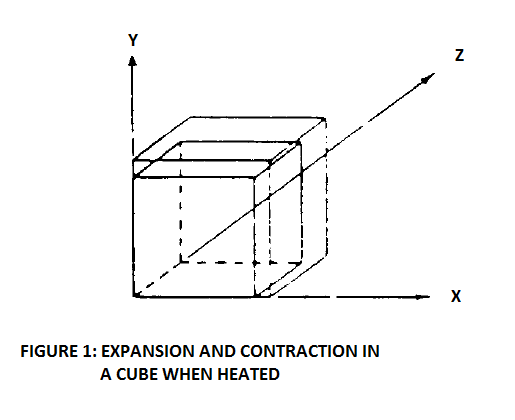
Now, assume that this cube is restricted from expanding in x-direction (that is, along x-axis) by placing it between two wedges. The cube would then only expand in y-direction and z-direction during heating.
During cooling, the metal wants to contract uniformly, that is – by the same amount in all directions. So, it contracts along all three axes, including the x-axis. Remember that the expansion during heating had only occurred along the y and z axis.
We see that a permanent reduction in length along the x-axis is the result. The cube thus gets permanently distorted, or deformed.
Something very similar happens during the welding too. Let us see an example of butt welds.
Distortion In Butt Welds
Let us see how distortion would happen in a butt weld between two plates. The understanding can then be stretched to all other kinds of welds.
In butt welds, the weld assembly is not uniformly heated/cooled. The weld zone area receives intense heat during welding, while the remaining portion of the base metal is cooler. The molten metal in the weld area is in an expanded form, while the rest of the metal is not hot, and is occupying its normal volume.
The molten metal tries to push the base plate outward, which is prevented by tack welds, stiffeners, etc.
During cooling too, the molten metal solidifies and shrinks, while the surrounding metal does not have to do so. The molten metal tries to shrink, but is resisted by the base metal because fusion has happened between base metal and weld metal. So the weld metal tries to pull base metal along with it.
If the base metal is not restrained at its outer edges by restraints, it would respond to this pull by getting distorted in the angular direction, because that is the easiest movement available.
The amount of distortion or weld deformation depends on the volume of weld metal (a larger pool of weld would exert a greater pull), coefficient of thermal expansion α (a greater α would mean greater reduction in volume during cooling, therefore a greater pull), extent of resistance available (by stiffeners, clamps, already deposited underlying weld metal, etc.) to deformation, and a few other factors, which we shall see in the Factors Affecting Distortion later in this article.
An angular distortion is thus the result, as can be seen in the figure below.
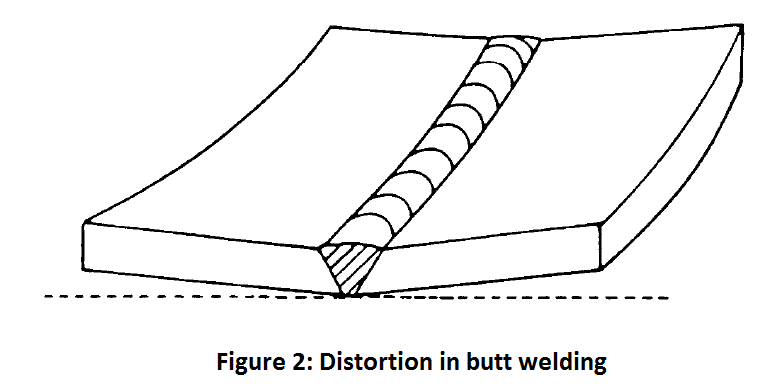
If the base metal is not free to deform in such angular fashion because it is prevented from doing so by restraints at the outer edges of the assembly, it would try to respond to the pull of the shrinking weld metal by distorting in any other direction available.
This produces warping in the plate, and is generally observed in thin base metals. That is why welding sheet metal without warping is a challenge.
If the base plate is heavily restrained from all ends, the deformation is prevented at the time of welding. However, a stress develops inside the weld assembly, which would try to relieve itself once the restraints are removed.
In such welds, the distortion or warpage can occur once the restraints have been removed after completion of the welding. Thin base metals are susceptible to this kind of distortion.
If the base metal is thick, and has been prevented from distorting by use of heavy restraints, clamps and stiffeners, the shrinking weld metal still imposes stresses on the metal, which cannot now be relieved by deforming. [Although slight deformation can still occur after completion of welding (and removal of restraints), the large volume of solidified weld metal prevents any significant deformation.]
These stresses are left behind as a residue of welding, hence they are called residual stresses.
Residual stresses are not good for a weld. If the residual stress is lower than the yield point of the metal, it is mostly harmless, and does not produce any visible, immediate ill-effect on the weld. It can be relieved later on by methods such as thermal stress relieving (post-weld heat treatment), mechanical stress relieving, and so on.
If this residual stress is greater than the yield point of the metal, the metal would yield. This deformation is called plastic deformation (as opposed to elastic deformation), because the distortion is permanent. The result of this can be development of a crack, or warpage of the plate.
Types of Distortion
Angular Distortion
This is the most common type of distortion that we come across. Angular distortion causes bending in transverse direction, as illustrated in the figure below.
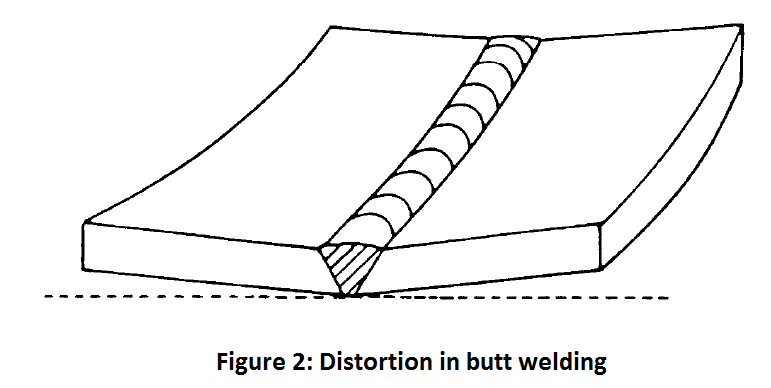
Longitudinal and Transverse Distortions
Imagine a butt joint being welded, as shown in the figure below. As welding progresses along the length of the plate, the bead that was deposited first gets solidified first. This solidified bead then resists the shrinkage of the later portions of the bead. The portion deposited first is pulled in tension in the longitudinal direction, by the bead deposited later.
This is illustrated in the figure below.
Longitudinal distortion affects the length of the weld assembly, although – not by much.
Likewise, in a butt weld – the solid base metals (since they are held in place by clamps, or by root passes) resist the transverse shrinkage of weld metal. This produces residual stresses in the transverse direction, as indicated in the figure below.
Transverse distortion affects the width of the weld assembly.
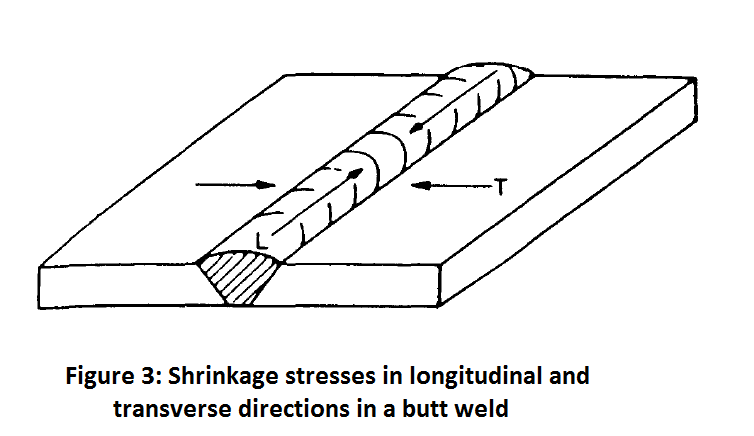
Shrinkage stresses in a fillet weld occur similarly as explained above, as shown in the figure below.
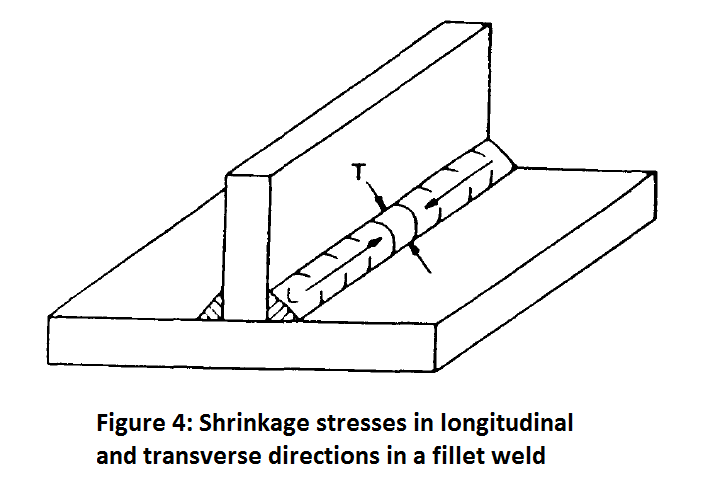
Distortion In Fillet Welds
As explained above, shrinkage stresses occur in fillet welds as well, in a manner similar to that in butt welds. The exact nature of distortion in a fillet weld is difficult to predict because fillet welds are generally used in combination with other welds. The following figure illustrates typical distortions found in a fillet welds.
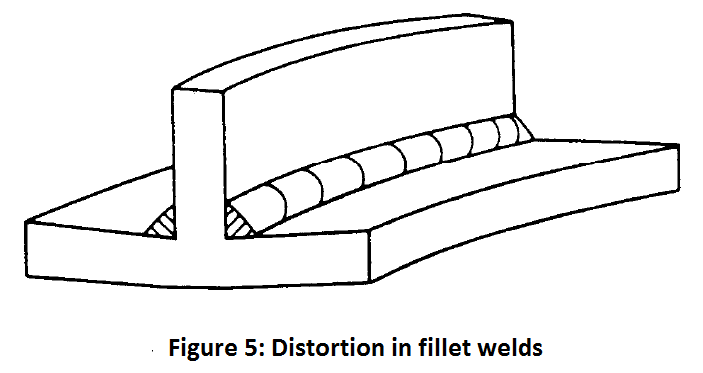
Factors Affecting Distortion Or Warpage In Welding
There are several factors that affect the extent of distortion or warpage that occurs in welding. Any strategy that addresses the question ‘how to avoid warpage in welding’ must take these factors into consideration. Some of them are as follows:
1. Base Metal Properties
The coefficient of thermal expansion, and thermal conductivity, – play an important role in determining how much distortion will occur.
Coefficient of thermal expansion (α) is a measure of how much the metal would expand (or contract) when it undergoes a temperature change. Different metals have different properties, hence the value of α is different for every metal. For example, stainless steel has a higher α’’ than carbon steel.
A higher α indicates the metal will expand/contract by a larger volume on heating/cooling. So, a metal having high α can be expected to have higher shrinkage stresses, and thus higher amounts of warping in welding.
Thermal conductivity (denoted by letter ‘K’) is a measure of how fast the heat conducts (or flows) through a metal. A higher ‘K’ indicates the ability of metal to quickly conduct heat through its volume.
The temperate differential is determined by thermal conductivity. The higher the thermal conductivity of the metal, the less effect differential heating will have.
For example, the thermal conductivity of copper is the highest, aluminum is half that amount, and steel is about one-fifth that of copper. Heat would move more quickly through a copper bar than through a steel bar, and the temperature differential would not be so great.
This physical property must be considered when welding, along with the fact that arc temperatures in most arc welding processes are very similar but the metal melting points are somewhat different.
A metal having higher ‘K’ would be able to vacate the heat generated in the weld zone quickly to the surrounding volume of metal. This would prevent a large temperature differential from forming across the base metal being welded.
Such metals would not have too much differential heating/cooling across its volume, and can thus be expected to have lower amounts of distortion during welding.
2. Restraint in the joint
If a joint is not restrained in any direction, it distorts itself to relieve the thermal stresses generated during the welding. In order to prevent this, physical restraints, such as stiffeners at the back side of a butt joint, clamps on the sides, etc., are generally used to prevent distortion from occurring.
However, this has a downside too. A highly restrained joint would have higher residual stresses in it. High amounts of residual stress in the weld is bad for the joint. In such welds, distortion must be controlled by other methods, besides restraints.
3. Joint Design
A butt weld when welded from only one side can be expected to have considerable angular distortion. A double welded butt joint (welded from both sides – front and back) would have lower angular distortion, because the distortion produced while welding from the back side would try to equalize the distortion produced during welding from the front side.
Welding from the back side is of course not always possible due to lack of access to the back side of the joint. In such cases, other ways of controlling distortion should be adopted.
4. Weld Procedure
A higher root gap would entail greater volume of weld metal, and therefore more shrinkage of metal, and thus higher chances of distortion.
Weld sequence also substantially impacts distortion. For example, in a thick double welded butt joint, welding alternatively at front and back can minimize the angular distortion.
In circumferential seam joints where concentricity of the two shells being welded is a critical requirement, special weld sequence should be adopted in the welding of the cir-seam joint.
If one starts at point and keeps on proceeding along the circumference without any weld sequencing, the shells can quickly distort and the concentricity of the two outer ends of the shell will go astray.
So, one must adopt a distributed weld sequence around the periphery, especially in the start of the joint. This will equitably distribute the heat around the circumference, and will keep distortion to a minimum.
Equitable distribution of heat is the key while deciding the weld sequences aimed at minimizing distortion and warping in welding joint. See more of this in the following paragraphs.
How To Control Distortion In Welding?
How to prevent warping when welding – is a question that must be addressed by not just the welder, but also the welding engineer. The skill of the welder is important, however the design of the weld also goes a long way in determining how to weld without warping in a joint.
Completely eliminating it is probably difficult, however it can be controlled.
Distortion can be controlled by several methods.
One of the methods is to pre-position the work-pieces before start of welding. This pre-positioning should be done in a direction opposite to the direction in which the distortion is expected to occur. This ensures that the distortion leaves the joint in the desired shape after the welding.
Another method is to restrain the work-pieces physically, by placing clamps, fixtures, stiffners, etc. The part is prevented physically from getting distorted. However, the use of restraints should be moderate. Use of too much restraints may invite cracking in the joint. Restraints should be used in combination with other methods.
Another method is to design the joints in such a manner that the heat is distributed equally on either side of the centreline of the part.
The selection of process also influences the distortion. A heavy heat input process like submerged arc welding, for example, is not suitable for base metals of ¼ inch (6.4 mm) thickness.
Another important method is weld sequencing. The joint can be welded in accordance with a sequence that distributes and spreads the heat.
Another method, although a less preferred one, is to correct the distortion mechanically, after it has occurred. Or, straightening can be achieved by thermal or application of a flame too.
If someone asks how to fix weld distortion, the answer must involve these above methods or a combination of these. Also, warpage due to welding can be reduced by keeping a few other factors in mind.
While welding, the following factors should be considered by the welder in order to reduce welding warping:
- Neutral axis of the part should be located, and welder should seek to distribute the heat evenly around the neutral axis.
- The location of beads, size of beads, and distance of beads from neutral axis should seek to distribute the heat evenly on all sides of the neutral axis.
- The welding technique should be varied based on the warpage observed in the first few passes.
- The distortion observed after the first few passes should guide the weld sequence of the subsequent passes.
Controlling Distortion In Large Structures
Let us see now how to keep metal from warping when welding in large structures. It is important to establish a procedure to minimize distortion, in welding of large structures. The sequence of joining plates on a deck or on a tank can significantly affect the stresses and warpage in the structure.
As a general rule, it is advisable to make transverse welds before longitudinal ones. The figure below illustrates a suggested sequence for the part shown.
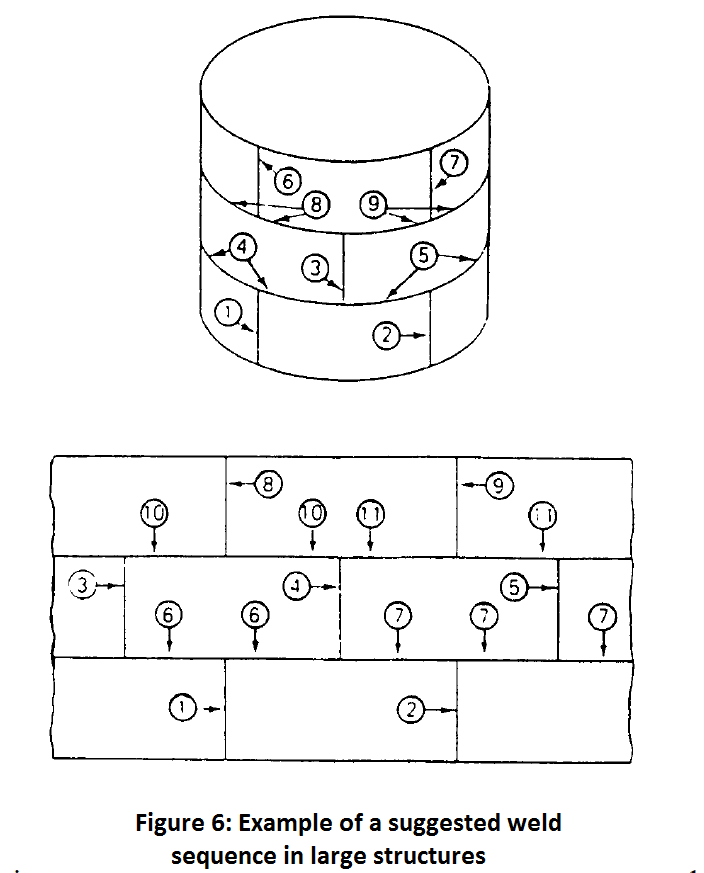
Controlling Warpage In Smaller Structures
What should be done to prevent warpage or distortion in welding of small parts such as sheet metal? Several techniques, individually or in combination with others, can be applied for controlling distortion in welding of smaller structures. Below are a few of the techniques.
- Strong backing and restraining fixtures should be used. Use of multiple tack welds is helpful.
- Heat sinks are used to achieve fast cooling of welds.
- Pre-positioning of the parts may be done so that the joint achieves the desired shape after distortion.
- Balancing of heat around the neutral axis by using a calibrated weld sequence.
- Use intermittent welding so that welding is slow, and heat input to the part can be spread over time.
- Use correct joint design and select appropriate welding procedures.
- Use pre-heat sparingly.
Residual Stresses And Welding Distortion
Residual stresses are detrimental to a weld. They can cause premature failure of a weld.
Distortion, as we saw in the above paragraphs, results due to shrinkage of weld metal. When a metal is not allowed to distort by the use of clamps, etc. residual stresses are the result.
Residual stresses and distortion affect joints by contributing to buckling, curling, and cracking at low loads than would be expected otherwise. Due to the presence of residual stresses, buckling may occur at a lower compressive load than would occur normally.
In tension, residual stress may lead to running brittle cracks that can spread to low stress areas. Residual stress also contributes to fatigue failures and corrosion failures.
How To Reduce Residual Stresses In Weldments
Residual stresses can be minimized by both thermal methods and mechanical methods.
The thermal methods means post weld heat treatment (PWHT) of the weld. This PWHT relieves the stresses locked inside the weld, hence it is also called stress relief heat treatment. In the course of heat treatment, the metal is taken to a high temperature.
The yield strength of the material at this high temperature is lower than that at room temperature. The material therefore yields to the residual stresses present inside the body of the metal, and thus the stresses are relieved. The heat treatment also affects the mechanical properties of the weldment.
The heat treatment not only relieves the residual stresses inside the weldment, but also softens up the hard heat affected zones of the weld. This improves the toughness of the microstructure, and improves overall brittle fracture resistance of the joint.
The residual stresses can be reduced by mechanical methods as well. These methods include peening, proof dressing, etc. These methods do not affect the hard heat affected zone of the weld.