This article talks about the basics of tig welding, starting from what is tig welding, the principles of tig welding process, shielding gas used in tig welding, and advantages of tig welding.
What is TIG Welding?
TIG welding is also called Gas Tungsten Arc Welding. It is a welding process in which joining of metals is achieved by heating the metal with an arc. The arc is struck between a tungsten electrode and the work-piece. The tungsten electrode is non-consumable.
Shielding is obtained by using an inert gas, often argon. The filler metal is added separately, often fed into the molten metal using hand.
The process derives its name from three main characteristics of the process – gas shielding, tungsten electrode, and an electric arc. Hence the name gas tungsten arc welding.
The tungsten electrode can be pure tungsten or an alloy. Small quantities of lanthanum and cesium are added to make it suitable for the purpose.
The shielding gas is provided to shield the arc from atmospheric gases, and it is fed through the electrode holder.
Sometimes filler metal is not added. It is then called an autogenous weld.
What distinguishes TIG welding from other arc welding processes is that the arc is struck by a non-consumable electrode. The TIG welding torch is thus suitably designed to house the tungsten electrode. The torch also provides a passage for supply of inert gas.
TIG welding is most commonly used to weld stainless steel and non-ferrous metals such as aluminum, magnesium, and copper alloys; especially when thin sections are involved. TIG welding enables much greater control over the weld. More control than processes such as SMAW and GMAW paves the way for stronger, higher quality welds.
Preventing carbide precipitation during TIG welding of stainless steel is an important consideration that must be taken into account. When TIG welding a short arc length is maintained while preventing contact between the electrode and the workpiece. TIG welding normally requires two hands. This is because most applications require that filler metal be manually fed into the weld pool with one hand. The other hand is used to handle the TIG welding torch.
TIG Welding Process Principles
Before the commencement of welding, the surface must be cleaned. It must be made free of oil, grease, paint, rust, and contamination of any other kind. Cleaning can be done mechanically like using a grinder. Or, it can be done chemically using a cleaning agent such as acetone.
Striking The Arc
Striking the arc can be achieved by using any of the following:
- Touch the electrode monmentarily on the work-piece and withdraw it, similar to the stick welding.
- An apparatus that causes a spark to jump from the electrode to the work can be used.
- Thirdly, an apparatus that initiates and maintains a small pilot arc, providing an ionized path for the main arc to be struck can also be used.
When alternating current is used, high frequency arc stabilizers need to be used. When high frequency arc initiation is used, a low current-high voltage is super-imposed on the welding circuit. Basically, a high voltage is applied, while using little current.
High voltage causes the shielding gas between torch and work-piece to get ionized. The ionized medium is conductive to the electricity, and a small current is then enough to initiate the arc.
It must be noted that inert gases are otherwise not conductive. However, when they are ionized, they become a good conductor of electricity. In welding with direct current, the high frequency is cut-off immediately after arc is struck. However, while welding with alternating current, it remains active even after the arc is struck, especially when TIG welding aluminum.
Once The Arc Is Started
In manual TIG welding, the torch is held at an angle of 15° with the vertical, by the welder. When the mechanized TIG welding is being done, the torch is kept almost vertical to the work-piece.
Once the arc is struck, the torch is twirled a little in a small circle. This is done such that a small weld pool of molten metal appears. The end quality of the weldment depends on how expertly the weld pool is manipulated and controlled.
The filler rod is dipped into this weld pool. The rod melts and increases the size of the pool. Once the torch is moved a little ahead, the portion of the pool left behind solidifies. The pool moves a little ahead. Then, the next drop of molten metal is added by dipping the filler rod in the pool. The weld pool thus keeps proceeding, while leaving behind a trail of solidified weld metal. A properly made weld is characterized by appearance of fine ripples on the bead.
Feeding The TIG Welding Rod In Weld Pool
It is important that the movement of torch and filler is synchronous and smooth. It is essential that the shielding is continuous and comprehensive. A rough motion can allow surrounding air to contaminate the weld metal and heat affected zone.
The rate of shielding gas should be optimum. It should be just enough to obtain sufficient shielding of the arc. Too much of it can bring turbulence around the weld pool which results in a poor looking weld. The usual choice of shielding gas is argon.
The TIG welding rod is usually held at an angle of 15° with the horizontal. It is fed slowly into the molten weld pool with smooth movement of hand. The hot end of this rod should not be suddenly removed from the cover of shielding gas. Else, the tip – which is in molten state can get oxidized by the atmospheric gases.
Another approach is to press the rod against the work-piece, just at the edge of the molten pool. This method is used when doing multiple pass welding of groove joints.
A third approach is to continuously oscillate the welding rod and arc from side to side, while feeding rod into the molten pool. This approach is used often in large welds. At any instant, the arc goes in one direction while the rod goes in another. However, the welding rod is near to molten pool at all times.
In automatic welding, the filler rod is continuously fed into the pool by a mechanized arrangement.
Welding Position
The welding position is determined by the condition of the job. The easiest, fastest, and probably the best position is of course – the flat position.
This position also gives highest joint penetration, and deposition rate of the weld metal. This is because large weld pool can be supported on the work-piece, unlike vertical position and overhead position. The appearance of the weld is pleasing to the eye.
In other positions such as vertical, overhead and horizontal, the weld pool must be of a smaller size. This is because the molten metal tends to sag because of gravity. Due to this, lack of fusion is a common problem in out of position welds. Although good penetration can be achieved by a skilled welder in vertical-up position too. But, the rate of deposition is undeniably slow in other positions in comparison to the flat position.
TIG Welding Filler Metals
TIG welding can be performed with the use of filler metal, and without it as well. Thickness of the base metal and joint design determine whether or not filler metal needs to be used.
When filler metal is used, adopting correct technique of feeding it into the molten pool is necessary. It requires practice before one can deposit quality welds.
The technique of feeding filler metal in the weld pool is illustrated in the figure below. Regarding the polarity , although TIG welding with DCEN is more commonly used, direct current electrode positive is also used.
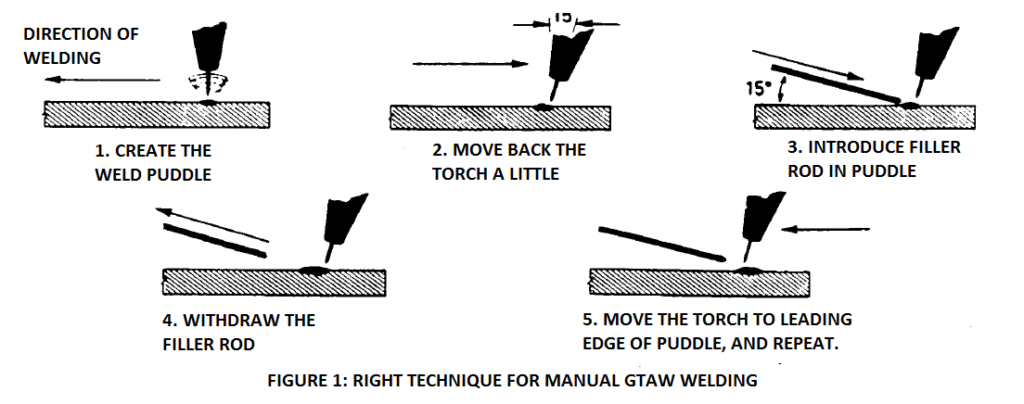
Stopping The Welding
When welding is required to be stopped, it can be done by stopping the inflow of current to the torch. This is done by turning to off switches that are provided for the purpose. These days, these switches are foot-operated.
These switches allow the welder to start, stop, and adjust the flow of current at any time.
One should never withdraw the torch suddenly from the molten pool. This is because this takes away the shielding cover of the inert gas. This cover is necessary to keep the molten metal and tungsten electrode from getting oxidized.
While stopping the welding, the current should be switched off first. The torch should be held in place hovering over the last bit of molten pool with the shielding gas on. This allows the molten metal and tungsten tip to cool down enough, and risk of oxidation is avoided.
What Kind Of Weld Joints Can Be Welded?
TIG welding is used for joints where a high quality of welding is required. Also, since this process is far slower than other processes, it is not suitable for thick sections. Also, some metals are best welded by TIG welding alone, such as titanium and zirconium.
Regarding joint designs, all standard joint designs such as tee-joint, lap-joint, corner-joint, edge-joint, fillet joints, butt-joints, etc. can be welded with this process.
For base metals of thickness below 1/8 inches (3.2 mm), it is not necessary to bevel the edges of the plate. For such low thicknesses, use of filler metal is also not very necessary. The welding engineer must make a decision based on all the conditions involved.
For thick sections, edge preparation of the base plates is, of course, mandatory. Also, use of filler metal is mandatory in order to fill up the grove.
Major Operating Variables Of TIG Welding
The main operating variables of TIG welding are:
- Welding current, voltage, and power source characteristics.
- Chemical composition of the tungsten electrode, its current carrying capacity, and angle of grinding on the tip.
- Shielding gas – argon, helium, or mixture of both, and its’ flow rate.
Filler metals are chosen generally to meet the chemical composition of the base metal being welded. In ASME BPVC, TIG welding filler rods are classified under SFA 5.18, SFA 5.9 and SFA 5.28 of ASME Section II, Part C.
TIG Welding Equipment
The following paragraphs talk about basic features of TIG welding equipment, TIG welding equipment parts, and TIG torch nomenclature.
Basic Features Of TIG Welding Equipment
The basic components that form a part of TIG welding equipment are shown in the figure below:
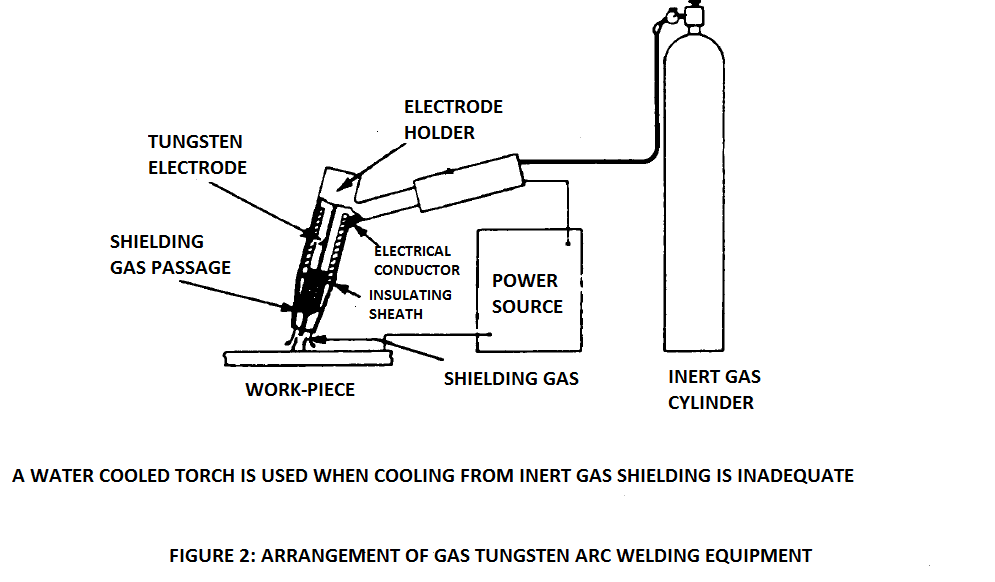
The major components involved in GTAW welding are as follows:
(1) the welding machine, which houses the power source
(2) the electrode holder and the tungsten electrode
(3) the shielding gas cylinder and it’s controls
(4) Several optional accessories, chief among which is a foot rheostat to control the current while welding. Other accessories include water circulating systems for water cooling the electrode holders; and arc timers.
Modern day TIG welding machines are quite sophisticated. They are specifically designed for TIG welding, and come with in-built frequency generators. They can operate on both direct current as well as alternating current.
The machine on its own controls the flow rate of shielding gas. And it automatically circulates the cooling water to the torch if the torch is water cooled. The electrode holders are so designed such that tungsten electrode and gas nozzle can be easily replaced when they are worn out or damaged.
The machines for mechanized welding come with higher level of sophistication. These machines come with in-built mechanisms to handle the work pieces, and to initiate and control the arc. Provision is also given to feed the filler at a regulated rate. And to also regulate the flow rate of shielding gas and cooling water.
TIG Welding Equipment Parts
A schematic of the parts of TIG welding equipment is shown in the figure below.
Besides the equipment shown, the personnel protective equipment (PPEs) form an equally integral part of the TIG welding equipment. The PPEs protect the welder from the harmful rays emanating from the arc. These rays can damage the eye sight if eyes are allowed to expose to them directly.
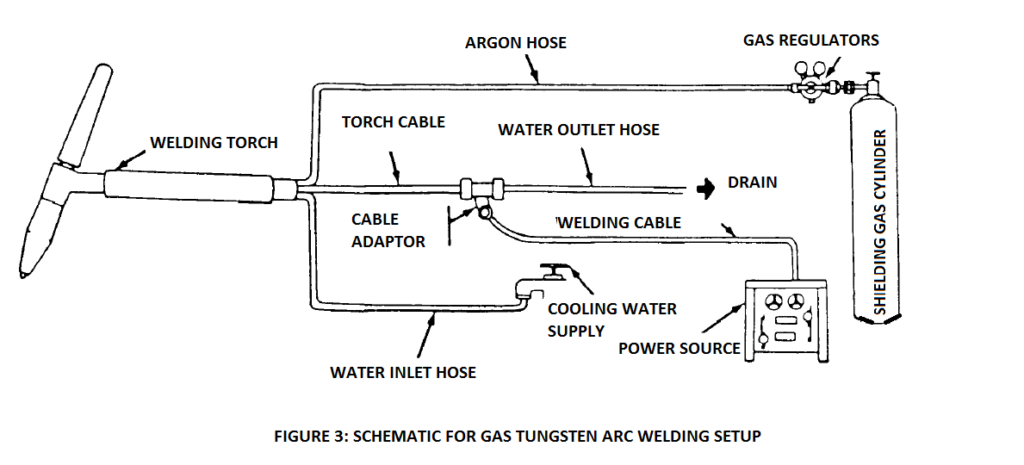
The modern day machines have both water cooled and air-cooled torches. Each can support different amperage ratings. The machine’s manual must be consulted before taking up the machine for welding.
The shielding gas for TIG welding is commonly argon gas. It is generally supplied stored in gas cylinders of capacity around 330 cubic feet, at a pressure of 2000 psi. This pressure falls as the gas is drawn out for welding. A pressure regulator is mounted on these cylinders to regulate the flow of gas. The regulator also indicates the existing pressure inside the cylinder.
Regulators are combined with flow meter. They come in pairs. The flow meter is a device that indicates the rate of flow of argon in cubic feet/hour or litres/minute. A schematic of a common regulator-flow meter is shown in the figure below.
The flow of argon to the welding torch is regulated by turning the adjusting screw on the pressure regulator. The rate of flow is specified on the WPS. It depends on the size of filler metal, type of base metal being used, and its’ thickness.
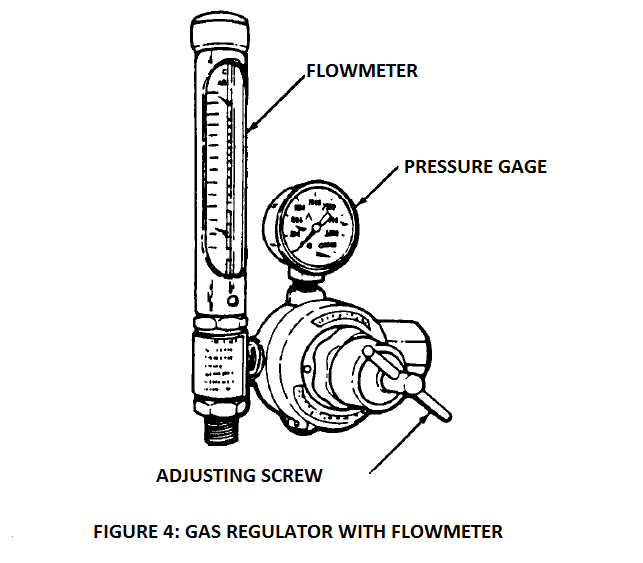
The shielding gas flows through the electrode holder, and envelopes the arc from all around. Argon is 1.3 times heavier than air. So, it displaces the air surrounding the arc region, and lies like a blanket over the weld pool. It thus protects the arc, molten puddle, and heat-affected zone from getting oxidized by the atmospheric gases.
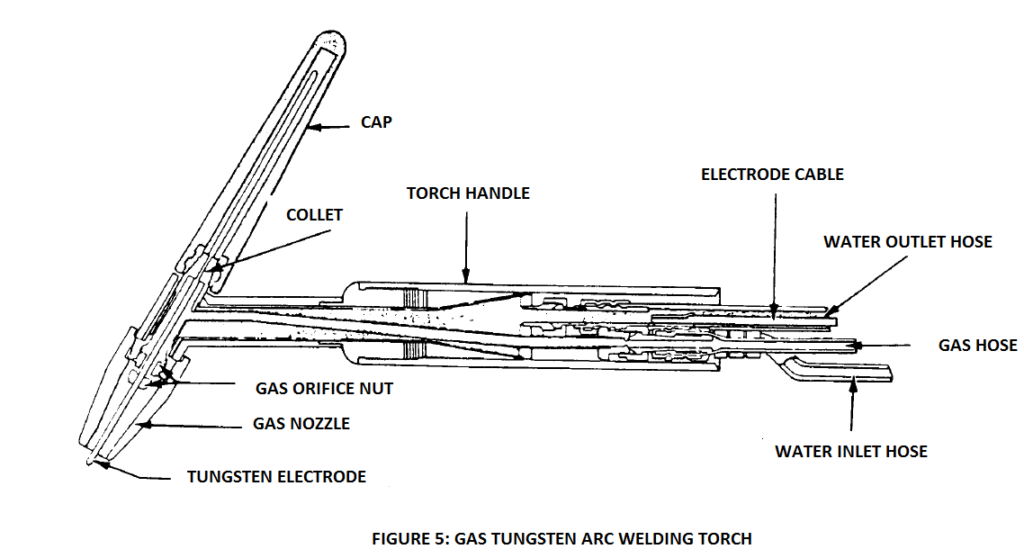
The welding torch gets heated up due to the current flowing through it. Heating of the torch also occurs due to the heat of the arc. It therefore needs to be cooled. Water cooled torches employ normal water to get the cooling effect. The water must be clean; else dirty water can clog the passages. This can open up the torch to the risk of getting overheated during welding, and getting damaged.
In order to prevent external particles from contaminating the water, a water strainer is used at the water inlet. If the welding is being carried out in freezing weather, and the machine is a self-contained unit, wherein a pump is used to re-circulate the water from a surge tank, an antifreeze unit is installed in machines to keep the water from getting frozen.
TIG Torch Nomenclature
See the figure above showing a TIG welding torch.
(1) TIG Torch cap: It locks the tungsten electrode in place, and prevents the gas from escaping outside.
(2) TIG Torch collet: It is made of copper. When the tungsten electrode fits inside and the cap is tightened, it squeezes against the tungsten electrode and locks it in place.
(3) TIG Torch gas orifice nut: permits the shielding gas to flow out from the torch and on to the work-piece.
(4) TIG Torch gas nozzle: Increases the velocity of gas by contricting the cross section area for the flow. Focuses the flow of gas on to the weld puddle. Generally it is made of ceramic. However, for heavy duty applications, it is made of copper and has to be cooled by an envelope of water-cooling.
(5) TIG Torch hoses. Three plastic hoses run inside the torch. One carries shielding gas. The other two carry water for cooling the torch, and second carries the current for doing the welding.
Things To Keep In Mind When TIG Welding
TIG Welding Process requires careful keeping in mind of several things, if good quality is important. These factors include torch angle, filler metal angle, grinding the tungsten electrode for preparing it for welding.
TIG Torch angle
Position TIG torch about an 1/8 of an inch from the surface. Once an arc is established, angle the torch about 15 to 20 degrees away from the direction of travel.
Filler Material Angle
When filler material is needed, dab the filler rod as low as possible. This is required to avoid touching the tungsten and contaminating the weld. Torch melts base material and the base material melts your filler rod.
Tungsten Grinding / Preparation For Mild Steel, Stainless Steel And Chromoly Steel
- Use a diamond grinding wheel to achieve a good finish with a sharp point. This also means less wear of the grinding wheel.
- When grinding tungsten, hold the rod parallel, rather than perpendicular. This ensures that the grind marks are running the length of the tungsten instead of across it. This aids the flow of current down the electrode.
- Slowly rotate the tungsten to form a point similar to sharpening a pencil. The finished point should be less than 2.5 times the diameter of the electrode.
- For TIG Welding aluminum, grind off the point of the tungsten to create a flat spot.
- After grinding the tungsten place it into the TIG torch, sticking out about 3/16 to a 1/4 of an inch.
TIG Welding Shielding Gas
With the TIG welding process, shielding gases are required to protect the welding area from gases in the atmosphere . These gases mainly include oxygen and nitrogen. These gases can create fusion defects, porosity, and embrittlement in the metal to be welded, if they come in contact with the welding metal, electrode or arc. The shielding gas also transfers heat from tungsten electrode to the metal and helps start and maintain a stable arc.
The selection of a TIG welding shielding gas depends on a number of factors. These factors include the type of metal to be welded, joint design, and desired final weld bead appearance. Argon is the shielding gas most often used for TIG welding because it helps prevent weld defects due to a varying arc length. When used with alternating current, the use of argon results in a high-quality weld with a good appearance.
Helium is sometimes used as a TIG welding shielding gas. This is done to increase weld penetration, welding speed. And to weld metals with high heat conductivity, such as copper and aluminum. A significant disadvantage when using Helium as a shielding gas is the difficulty of striking an arc with helium gas. Another disadvantage is the decreased weld quality associated with a varying arc length.
Argon-helium mixtures are also sometimes used as a TIG welding shielding gas. The combined gases can increase control of the heat input while maintaining the benefits of using pure argon. Argon-helium shielding gas mixtures are often made with about a 75% or higher concentration of helium and the balance argon.
These mixtures increase speed and quality when TIG welding aluminum with Alternating Current(AC). Also, they make it easier to strike an arc.
TIG Welding Advantages
TIG welding is the most preferred method of welding for non-ferrous metals. Especially metals such as aluminium, nickel-base alloys, titanium, zirconium, and stainless steel.
The quality of welding produced by TIG welding is very high. Broadly speaking, some of the tig welding advantages include:
More precise control of the weld, since the arc and filler rod are independently controlled.
No smoke and fumes are produced during the welding. Unlike SMAW, there is no spatter that must be cleaned between the passes. Likewise, there is no slag on the weld.
TIG welding is quite suitable for welding thin metals because of high control in the hands of welder. This allows the welder to distribute heat across the weld. For thin metals, autogenous welding is also possible, which cannot be done in other processes like SMAW, SAW, GMAW, etc.
TIG welding also has less distortion due to a concentrated heat source.
TIG welding can be used on almost all metals. Although it is not preferred for a few low meting point metals such as zinc. It is extremely useful for welding of highly reactive metals like titanium and zirconium. These metals cannot be welded by any other process.
Also, TIG welding is a highly preferred process of welding for welding of aluminium and magnesium.
Critical service applications which make use of reactive and expensive metals such as titanium demand thorough cleaning of the weld surface before commencement of the welding.
Let us see the TIG welding advantages in some detail:
TIG Welding = A Concentrated Welding Arc
The TIG welding arc is concentrated. This enables pinpoint accuracy and complete control of heat input to the workpiece. That results in a much smaller heat-affected zone.
The high concentration of heat is an advantage when welding metals with high heat conductivity. Especially metals such as aluminum and copper, which readily disperse the heat applied to the base metal. A smaller heat-affected zone is an advantage when TIG welding. This means that a very small portion of the joint is coarse grained and brittle.
The heat-affected zone is where a welded joint is weakest. It is the area along the edge of a weld bead that is most likely to break during destructive testing. The enhanced articulation of the TIG welding electrode enables finer control of the welding puddle.
TIG Welding = No Slag
With the TIG welding process, there is no requirement for flux. Therefore, there is no slag to obscure the welder’s vision of the molten weld pool. The finished weld will not have slag to remove between passes. Entrapment of slag in multiple pass welds is rarely seen.
TIG Welding = No Sparks Or Spatter
In the TIG Welding process, there is no transfer of metal across the arc. There are no molten globules of spatter to contend with. Also no sparks are produced if the material being welded is free of contaminants. Also under normal conditions, the TIG welding arc is quiet. It operates without the usual cracks, pops, and buzzing of SMAW (or Stick welding) and GMAW (or MIG). Generally, the only time noise will be a factor is when pulsed arc or AC welding mode is being used.
TIG Welding = No Smoke Or Fumes
The TIG welding process itself does not produce smoke or injurious fumes. If the base metal contains elements such as lead, zinc, nickel, or copper that produce fumes, these must be dealt with. Just as in any fusion welding process on these metals. If the base metal contains oil, grease, paint, or other contaminants, smoke and fumes will definitely be produced as the heat of the arc burns them away. The base material should be cleaned to make the conditions most desirable.
TIG Welding Disadvantages
TIG welding is an uneconomical method of welding. This is considering that the rate of metal deposition is far lower than other methods of welding. Some of the disadvantages the GTAW process are:
- The process is slower than other arc welding processes such as SMAW, SAW etc. The rate of weld metal deposition is far lower.
- Care must be taken not to transfer molten tungsten from the electrode to the weld area, which causes contamination. The resulting tungsten inclusion is hard and brittle.
- If the filler rod is exposed to air in red hot condition, and then reintroduced in weld pool, metal oxides get introduced in weld metal.
- The shielding gases such as argon add to the cost of welding. Some metals such as titanium require only argon, and of very high purity. This comes at a price.
- The equipment for TIG welding is more sophisticated than SMAW process, considering the high frequency starter and all. This takes the equipment cost higher.
- Another disadvantage is that the hand-eye coordination necessary to accomplish the weld is more difficult to master. It requires a great deal of practice to become proficient in.
- The arc rays produced by the TIG welding process tend to be brighter than those produced by Shielded Metal Arc welding (SMAW ) and MIG welding or Gas Metal Arc Welding (GMAW). This is mostly due to the absence of visible fumes and smoke.
- The increased amounts of ultraviolet rays from the welding arc also cause the formation of ozone and nitrous oxides. You should take abundant care to protect your skin with the proper clothing. And protect your eyes with the correct shade lens in your welding helmet.
- When welding in confined areas, concentrations of shielding gas, like Argon may build up. And argon being heavier than air it will displace oxygen. Make sure to ventilate these areas properly.
Due to the above reasons, TIG welding is not a commercially competitive option for welding. This is especially so when the section thickness is high. If you can weld a metal with other processes such as SMAW, GMAW, SAW with adequate quality required for the application, then choosing TIG welding is not a wise option.
TIG Welding Versus MIG Welding
Gas shielding characterizes both processes. However there are a few notable differences.
Machines
MIG welding machines can make quick work of those around the house projects. With a basic configuration, you can setup your MIG welding machine with “gasless” filler material commonly known as “Flux Core“. It welds ok. But, if you want “clean” results you need a bottle of Argon/Co2 75/25% mix and “bare” filler wire.
In the advertising literature and instruction manual, it may say that you can weld aluminum. However, you need to change the wire feed rolls and replace the Steel Gun Liner with a frictionless plastic liner. Else you need to utilize a MIG welding attachment called a “spool gun”. You also need to get a new bottle of 100% Argon for welding aluminum.
Now that you have made the changes to your welding system, purchased or leased the additional gas bottle, and changed the filler wire to aluminum, you are now, in theory, ready to begin welding aluminum. Once you pull the trigger, the results may quickly surprise you to the point of disillusion.
The reality is, MIG (metallic inert gas welding) is very easy to learn when applied to steel applications. The less expensive machines, (under $500.00) typically do not have precise controls. So these are difficult to “tune in” to thin materials, (under 16 gauge). They also are not good for material in excess of 1/8″. Therefore, your window of opportunity with the basic setup is 1/8″ to 1/4″ steel.
TIG welding on the other hand is slower and requires some skill to come out successful. Take TIG welding of aluminum for example.
The welding of aluminum is where the TIG welding process, commonly known as “Heliarc” provides plenty of benefits. It allows you to weld most weldable materials. This includes 4130 Cr-Mo, Stainless, Aluminum, Titanium, Magnesium, as well as many other materials using only Argon gas.
Not only can you weld a variety of materials, but with the variable foot control you can precisely adjust your welding amperage on the fly. Also, you can weld super-thin materials, typically as thin as 24 gauge. Alternating current is better for general-purpose work since it provides the half-cycle of cleaning action.
TIG welding with square wave alternating current offers still greater cleaning action. However, joint design and technique must be adjusted.
Skill And Speed
TIG welding does require more skill. The weld deposition rate is low. Also, you need to be especially careful about keeping everything very clean. Exposure of the hot filler rod to air using improper welding techniques causes weld metal contamination.
Very much like Oxy-Acetylene gas welding procedures, you have to manually apply or “dab” filler material into the puddle using cut length alloys in the diameter of your choice.
The TIG torch provides the heat source through a tungsten electrode. You have to hold the tungsten electrode directly above the area you are welding. Depress the “foot control” (very much like a car accelerator) until you see a “liquid” puddle.
Dab the filler metal into the base of the puddle, (not the middle). Move at a slow consistent speed, dabbing the puddle as you go. This method of welding is slower than MIG. However, cold lapping is virtually non-existent with TIG, whereas it is somewhat common in MIG.
TIG welding machines are now smaller, and come at a lower cost. Power requirements are 115V and 220V and typically require no more than a 50 amp circuit.
TIG Welding Process Summary
TIG Welding is a clean process. Also, this process is desirable because of the advantages outlined. When TIG welding, the welder must maintain excellent welding conditions. The welder can do this by properly cleaning material, using clean filler metal and clean welding gloves. Also, he must keep oil, dirt and other contaminants away from the welding area.
Cleanliness when welding cannot be overemphasized, especially when welding aluminum or magnesium. These metals are more susceptible to contaminants than are ferrous metals.
Hydrogen in aluminum welds causes porosity.
For this reason, it is very important to eliminate all sources of hydrogen contamination. Sources such as moisture, and hydrocarbons that come in the form of oils and paint.
So this was about TIG welding. Would you like to add something? Please feel free to leave your thoughts in the comments section below.